Fleet Management
Developing the Fleets of Tomorrow: Where Innovation Meets Excellence
Our Fleet Management services are designed to enhance rail operations and the customer experience while optimizing the bottom line. We achieve this by helping our clients to develop robust maintenance strategies, plan and implement efficient and effective rolling stock procurement, and perform fleet modernization projects.
With experience spanning multiple continents and industries, we understand the pivotal role of maintenance in delivering top-tier services and optimizing costs. By analyzing maintenance procedures and results and implementing performance management practices, we empower organizations to make data-driven decisions and achieve maintenance excellence. We leverage best practices and years of experience to guide clients through fleet planning and rolling stock procurement from start to finish.
We have successfully collaborated with major rolling stock and rail technology suppliers worldwide, completing extensive testing and ensuring efficient product implementation. We recognize that the passenger experience matters. Our Fleet Design services incorporate global research and recent innovations, operations and maintenance perspectives, and ridership guidance to create accessible, sustainable, functional, and innovative train interiors and exteriors.
At DB E.C.O. North America, we utilize a modern approach to Fleet Management, anticipating the increasing role of digital maintenance, the importance of sustainability, and the transformative power of design.
Our Services
Rolling Stock Maintenance Excellence
The Challenge
Maintenance excellence is key to delivering high quality and reliable services while optimizing the total cost of rolling stock ownership. Moreover, it is an important prerequisite for expanding service and increasing ridership.
Achieving maintenance excellence is not trivial and many rail and transit organizations are far from reaching this goal. Across the industry, 20-40% of delays can be attributed to poorly maintained trains, 50% of downtimes are the result of unoptimized spare-parts management, and over 20% of a typical rail fleet undergoes maintenance at any given time. Since maintenance makes up almost half of the total life cycle cost of rolling stock, it is a key contributor to passenger fares.
Our Service
Quality & Performance Management
Railway and transit organizations may choose to oversee maintenance contractors or perform maintenance in-house or as a service. Regardless of the approach, the implementation of effective quality management and performance management systems are crucial for successful, cost-effective rolling stock maintenance.
At DB E.C.O. North America, we help our clients with the development and implementation of quality management systems. We consider systematic planning, monitoring, and improvement of maintenance processes and implement best practices, standardize workflows, and perform training and development of maintenance personnel.
DB E.C.O. North America also implements performance management systems, which complement quality management systems by measuring and analyzing key performance indicators (KPIs), such as equipment reliability, availability, and maintenance costs, and their underlying driving factors. By closely monitoring these KPIs and using them to drive decision-making, railway and transit organizations can identify areas for improvement and make data-driven decisions about where to allocate resources.
We offer both quick and thorough maintenance performance assessments, resulting in a set of quantifiable improvement measures and investment opportunities. One of our favorite instruments in performance management is the introduction of regular performance dialogues throughout all levels of the organization.
Maintenance Strategy Development & Programming
We work closely with our clients to design tailored component-level maintenance strategies that are optimized to meet the specific lifecycle needs of their rolling stock. We consider operational needs, as well as supply chain and financial constraints. The objective is to improve the reliability of the equipment by moving from reactive maintenance towards preventive maintenance. This is typically achieved by optimizing planned maintenance schedules and by introducing condition-based and predictive maintenance approaches.
With the implementation of these improvements, the number of failures and unplanned maintenance events can be reduced, ultimately resulting in a decrease of reserve asset capacity. In the near future, digital maintenance will play an increasingly significant role, helping to reduce time-consuming manual labor in diagnostics, spare-parts management, scheduling, and maintenance execution.
Facility Development
Managing a rolling stock maintenance facility requires a comprehensive approach that involves effective planning, resource management, and regulatory compliance, as well as a commitment to ongoing improvement and innovation. We help clients to implement effective resource management strategies, including inventory management, workforce planning, and equipment optimization, as well as develop tailored training programs for maintenance staff. We also help railway companies to identify and use the right technologies such as predictive maintenance systems, digital twins, and data analytics to maximize the efficiency and effectiveness of maintenance activities.
Our Experience
Applying international best practices to the North American market and engaging our team of subject matter experts, DB E.C.O. North America supports clients in optimizing their maintenance organizations and processes. We leverage our experience at Deutsche Bahn who owns ~100 maintenance facilities and maintains a fleet of ~20,000 passenger railcars, multiple units, and locomotives, ~80,000 freight railcars, and, as a service, third-party owned rolling stock. Recently, Deutsche Bahn implemented a new state-of-the-art maintenance quality and performance management system, creating new, flexible maintenance capacities. Their current focus is digitalizing and automating maintenance.
Fleet Planning & Rolling Stock Procurement
The Challenge
Establishing clear objectives, comprehensive planning, consistent and early monitoring, and negotiation skills are key to any successful procurement process. Poorly defined requirements can result in fewer or low-quality bids, and the need to restart the procurement process, causing delays and additional expenses.
Without well-defined planning and early involvement, clients experience costly change orders, high operations and maintenance costs, and incorrect components. In addition to the management of the procurement process, it is important to have industry-specific expertise to define specifications, conduct market research, and evaluate suppliers. Since the procurement of rolling stock is not an everyday occurrence, additional expertise is important to supplement in-house personnel.
Our Service
At DB E.C.O. North America, we provide our clients with procurement expertise based on best practices derived from many years of successful rolling stock procurement, operations, and maintenance at Deutsche Bahn. Our rolling stock procurement process is designed to guide clients from start to finish and is centered around the strategy “Design, Build, Maintain, and Operate.”
Before a procurement is initiated, it is important to establish a solid understanding of the fleet requirements, maintenance capabilities, current and future operations, budget, and organizational goals. At DB E.C.O. North America, we ensure fleet decisions are made that support long- and short-term operations, consider total cost of ownership, and prioritize the customer experience.
Throughout each procurement, we focus on reliability, availability, maintainability, and safety. We begin with detailed planning, establish goals and safety targets, and define operational requirements. Throughout the procurement process, we consider the operating environment, adhere to applicable agreements, and identify and document risks. Once procurement options have been identified, we calculate and analyze life cycle costs and develop documents and contractual packages.
Our Experience
At DB E.C.O. North America, we leverage the experience of Deutsche Bahn who owns, operates, and maintains 21,000 route-miles of track, 5,400 stations, 5,400 trains, and 2,600 train control facilities. Deutsche Bahn has procured rolling stock, technology, and services from almost all major suppliers throughout the world. As users of these rail technologies, Deutsche Bahn knows the strengths and weaknesses of each. DB E.C.O. North America complements this unrivaled experience with the familiarity of North America’s regulatory landscape, specialized domestic requirements, and the intricacies of the local supply chain network.
Interior & Exterior Fleet Design
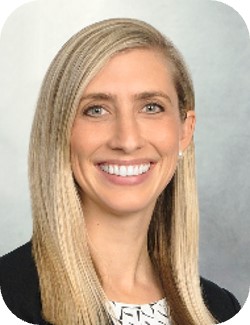